
联合国欧洲经济委员会条例No 13 (UN/ECE) —关于类别M、N和O机动车辆制动装置的统一规定 [2016/194]
技术法规类型:欧盟Eurlex法规 来源:tbtmap
EURLEX ID:42016X0218(01)
OJ编号:OJ L 42, 18.2.2016, p. 1-262
中文标题:联合国欧洲经济委员会条例No 13 (UN/ECE) —关于类别M、N和O机动车辆制动装置的统一规定 [2016/194]
原文标题:Regulation No 13 of the Economic Commission for Europe of the United Nations (UN/ECE) — Uniform provisions concerning the approval of vehicles of categories M, N and O with regard to braking [2016/194]
分类:11.30.40_与非政府国际组织的合作
文件类型:补充立法
生效日期:2015-10-08
废止日期:2058-12-31
法规全文:查看欧盟官方文件
18.2.2016 | EN | Official Journal of the European Union | L 42/1 |
Only the original UN/ECE texts have legal effect under international public law. The status and date of entry into force of this Regulation should be checked in the latest version of the UN/ECE status document TRANS/WP.29/343, available at:
http://www.unece.org/trans/main/wp29/wp29wgs/wp29gen/wp29fdocstts.html
Regulation No 13 of the Economic Commission for Europe of the United Nations (UN/ECE) — Uniform provisions concerning the approval of vehicles of categories M, N and O with regard to braking [2016/194]
Incorporating all valid text up to:
Supplement 13 to the 11 series of amendments — Date of entry into force: 8 October 2015
CONTENTS
REGULATION
1. | Scope |
2. | Definitions |
3. | Application for approval |
4. | Approval |
5. | Specifications |
6. | Tests |
7. | Modification of vehicle type or braking system and extension of approval |
8. | Conformity of production (COP) |
9. | Penalties for non-conformity of production |
10. | Production definitely discontinued |
11. | Names and addresses of Technical Services conducting approval tests and of Type Approval Authorities |
12. | Transitional provisions |
ANNEXES
1 | Braking equipment, devices, methods and conditions not covered by this Regulation |
2 | Communication |
Appendix 1 — | List of vehicle data for the purpose of Regulation No 90 approvals |
Appendix 2 — | Type approval certificate concerning the vehicle braking equipment |
3 | Arrangements of approval marks |
4 | Braking tests and performance of braking systems |
Appendix — | Procedure for monitoring the state of battery charge |
5 | Additional provisions applicable to certain vehicles as specified in the ADR |
6 | Method of measuring the response time on vehicles equipped with compressed-air braking systems |
Appendix — | Examples of simulator |
7 | Provisions relating to energy sources and energy storage devices (energy accumulators) |
8 | Provisions relating to specific conditions for spring braking systems |
9 | Provisions relating to parking braking systems equipped with a mechanical brake-cylinder locking device (Lock actuators) |
10 | Distribution of braking among the axles of vehicles and requirements for compatibility between towing vehicles and trailers |
11 | Cases in which Type-I and/or Type-II (or Type-IIA) or Type-III tests do not have to be carried out |
Appendix 1 |
|
Appendix 2 — | Alternative procedures for Type-I and Type-III tests for trailer brakes |
Appendix 3 — | Model test report form as prescribed in paragraph 3.9 of Appendix 2 to this annex |
Appendix 4 — | Model test report form for an alternative automatic brake adjustment device as prescribed in paragraph 3.7.3 of Appendix 2 to this annex |
Appendix 5 — | Trailer axle and brake information document with respect to the alternative Type-I and Type-III procedure |
12 | Conditions governing the testing of vehicles equipped with inertia (overrun) braking systems |
Appendix 1 |
|
Appendix 2 — | Test report on inertia-braking system control device |
Appendix 3 — | Test report on the brake |
Appendix 4 — | Test report on the compatibility of the inertia brake control device, the transmission and the brakes on the trailer |
13 | Test requirements for vehicles fitted with anti-lock systems |
Appendix 1 — | Symbols and definitions |
Appendix 2 — | Utilisation of adhesion |
Appendix 3 — | Performance on differing adhesion surfaces |
Appendix 4 — | Method of selection of the low-adhesion surfaces |
14 | Test conditions for trailers with electrical braking systems |
Appendix — | Compatibility of the braking rate of the trailer and the mean fully developed deceleration of the tractor/trailer combination (trailer laden and unladen) |
15 | Inertia dynamometer test method for brake linings |
16 | Compatibility between towing vehicles and trailers with respect to ISO 11992 data communications |
17 | Test procedure to assess the functional compatibility of vehicles equipped with electric control lines |
18 | Special requirements to be applied to the safety aspects of complex electronic vehicle control systems |
19 | Performance testing of braking system components |
Appendix 1 — | Model verification report form for diaphragm brake chambers |
Appendix 2 — | Model reference record of test results for diaphragm brake chambers |
Appendix 3 — | Model verification report form for spring brakes |
Appendix 4 — | Model reference record of test results for spring brakes |
Appendix 5 — | Trailer anti-lock braking system information document |
Appendix 6 — | Trailer anti-lock braking system test report |
Appendix 7 — | Vehicle (trailer) stability function information document |
Appendix 8 — | Vehicle (trailer) stability function test report |
Appendix 9 — | Symbols and definitions |
Appendix 10 — | Field test documentation form as prescribed in paragraph 4.4.2.9 of this annex |
Appendix 11 — | Vehicle (motor vehicle) stability function information document |
Appendix 12 — | Vehicle (motor vehicle) stability function test report |
20 | Alternative procedure for the type approval of trailers |
Appendix 1 — | Method of calculating the centre of gravity height |
Appendix 2 — | Verification graph for paragraph 3.2.1.5 — Semi-trailers |
Appendix 3 — | Verification graph for paragraph 3.2.1.6 — Centre axle trailers |
Appendix 4 — | Verification graph for paragraph 3.2.1.7 — Full trailers |
Appendix 5 — | Symbols and definitions |
21 | Special requirements for vehicles equipped with a vehicle stability function |
Appendix 1 — | Use of the dynamic stability simulation |
Appendix 2 — | Dynamic stability simulation tool and its validation |
Appendix 3 — | Vehicle stability function simulation tool test report |
22 | Requirements for the brake electric/electronic interface of an automated connector |
1. SCOPE
1.1. This Regulation applies to vehicles of categories M2, M3, N and O (1) with regard to braking (2).
1.2. This Regulation does not cover:
1.2.1. | Vehicles with a design speed not exceeding 25 km/h; |
1.2.2. | Trailers which may not be coupled to power-driven vehicles with a design speed exceeding 25 km/h; |
1.2.3. | Vehicles fitted for invalid drivers; |
1.3. Subject to the applicable provisions of this Regulation, the equipment, devices, methods and conditions enumerated in Annex 1 are not covered by this Regulation.
2. DEFINITIONS
For the purposes of this Regulation:
2.1. | ‘Approval of a vehicle’ means the approval of a vehicle type with regard to braking; |
2.2. | ‘Vehicle type’ means a category of vehicles which do not differ in such essential respects as:
|
2.3. | ‘Braking system’ means the combination of parts whose function is progressively to reduce the speed of a moving vehicle or bring it to a halt, or to keep it stationary if it is already halted; these functions are specified in paragraph 5.1.2. The system consists of the control, the transmission, and the brake proper; |
2.4. | ‘Control’ means the part actuated directly by the driver (or in the case of some trailers, by an assistant) to furnish to the transmission the energy required for braking or controlling it. This energy may be the muscular energy of the driver, or energy from another source controlled by the driver, or in appropriate cases the kinetic energy of a trailer, or a combination of these various kinds of energy;
|
2.5. | ‘Transmission’ means the combination of components comprised between the control and the brake and linking them functionally. The transmission may be mechanical, hydraulic, pneumatic, electric or mixed. Where the braking power is derived from or assisted by a source of energy independent of the driver, the reserve of energy in the system is likewise part of the transmission. The transmission is divided into two independent functions: the control transmission and the energy transmission. Whenever the term ‘transmission’ is used alone in this Regulation, it means both the ‘control transmission’ and the ‘energy transmission’. The control and supply lines between towing vehicles and trailers shall not be considered as parts of the transmission.
|
2.6. | ‘Brake’ means the part in which the forces opposing the movement of the vehicle develop. It may be a friction brake (when the forces are generated by friction between two parts of the vehicle moving relatively to one another); an electrical brake (when the forces are generated by electro-magnetic action between two parts of the vehicle moving relatively to but not in contact with one another); a fluid brake (when the forces are generated by the action of a fluid situated between two parts of the vehicle moving in relation to one another); or an engine brake (when the forces are derived from an artificial increase in the braking action, transmitted to the wheels, of the engine); |
2.7. | ‘Different types of braking systems’ means systems which differ in such essential respects as:
|
2.8. | ‘Component of a braking system’ means one of the individual parts which, when assembled, constitute the braking system; |
2.9. | ‘Continuous braking’ means the braking of a combination of vehicles through an installation having the following characteristics:
|
2.10. | ‘Semi-continuous braking’ means the braking of a combination of vehicles through an installation having the following characteristics:
|
2.11. | ‘Automatic braking’ means braking of the trailer or trailers occurring automatically in the event of separation of components of the combination of coupled vehicles, including such separation through the breakage of a coupling, the effectiveness of the braking of the remainder of the combination not being thereby destroyed; |
2.12. | ‘Inertia (or overrun) braking’ means braking by utilising the forces generated by the trailer's moving up on the towing vehicle; |
2.13. | ‘Progressive and graduated braking’ means braking during which, within the normal operating range of the equipment, and during actuation of the brakes (see paragraph 2.4.1 above);
|
2.14. | ‘Phased braking’ is a means which may be used where two or more sources of braking are operated from a common control, whereby one source may be given priority by phasing back the other source(s) so as to make increased control movement necessary before they begin to be brought into operation. |
2.15. | ‘Endurance braking system’ means an additional braking system having the capability to provide and to maintain a braking effect over a long period of time without a significant reduction in performance. The term ‘endurance braking system’ covers the complete system including the control device.
|
2.16. | ‘Laden vehicle’ means, except where otherwise stated, a vehicle so laden as to attain its ‘maximum mass’; |
2.17. | ‘Maximum mass’ means the maximum mass stated by the vehicle manufacturer to be technically permissible (this mass may be higher than the ‘permissible maximum mass’ laid down by the national administration); |
2.18. | ‘The distribution of mass among the axles’ means the distribution of the effect of the gravity on the mass of the vehicle and/or its contents among the axles; |
2.19. | ‘Wheel/axle load’ means the vertical static reaction (force) of the road surface in the contact area on the wheel/wheels of the axle; |
2.20. | ‘Maximum stationary wheel/axle load’ means the stationary wheel/axle load achieved under the condition of the laden vehicle; |
2.21. | ‘Electric regenerative braking’ means a braking system which, during deceleration, provides for the conversion of vehicle kinetic energy into electrical energy.
|
2.22. | ‘Hydraulic braking system with stored energy’ means a braking system where energy is supplied by a hydraulic fluid under pressure, stored in one or more accumulators fed from one or more pressure pumps, each fitted with a means of limiting the pressure to a maximum value. This value shall be specified by the manufacturer; |
2.23. | ‘Simultaneous lockup of the front and rear wheels’ refers to the condition when the time interval between the first occurrence of lockup of the last (second) wheel on the rear axle and the first occurrence of lockup on the last (second) wheel on the front axle is less than 0,1 second. |
2.24. | ‘Electric control line’ means the electrical connection between two vehicles which provides the braking control function to a towed vehicle within a combination. It comprises the electrical wiring and connector and includes the parts for data communication and the electrical energy supply for the trailer control transmission. |
2.25. | ‘Data communication’ means the transfer of digital data under the rules of a protocol. |
2.26. | ‘Point-to-point’ means a topology of a communication network with only two units. Each unit has an integrated termination resistor for the communication line. |
2.27. | ‘Coupling force control’ means a system/function to balance automatically the braking rate of towing vehicle and trailer. |
2.28. | ‘Nominal value’ definitions for braking reference performance are required to put a value on the transfer function of the braking system, relating output to input for vehicles individually and when used in combination.
|
2.29. | ‘Automatically commanded braking’ means a function within a complex electronic control system where actuation of the braking system(s) or brakes of certain axles is made for the purpose of generating vehicle retardation with or without a direct action of the driver, resulting from the automatic evaluation of on-board initiated information. |
2.30. | ‘Selective braking’ means a function within a complex electronic control system where actuation of individual brakes is made by automatic means in which vehicle retardation is secondary to vehicle behaviour modification. |
2.31. | ‘Reference braking forces’ means the braking forces of one axle generated at the circumference of the tyre on a roller brake tester, relative to brake actuator pressure and declared at the time of type approval. |
2.32. | ‘Braking signal’: logic signal indicating brake activation as specified in paragraph. 5.2.1.30. |
2.33. | ‘Emergency braking signal’: logic signal indicating emergency braking as specified in paragraph 5.2.1.31. |
2.34. | ‘Vehicle Stability Function’ means an electronic control function for a vehicle which improves the dynamic stability of the vehicle.
|
2.35. | ‘Subject trailer’ is a trailer representative of the trailer type for which type approval is sought. |
2.36. | The ‘brake factor (BF)’ is the input to output amplification ratio of the brake. |
2.37. | ‘Identification Code’ identifies the brake discs or brake drums covered by the braking system approval according to this regulation. It contains at least the manufacturer's trade name or trademark and an identification number. |
2.38. | ‘Axle group’ means multiple axles where the axle spread between one axle and its adjacent axle is equal to or less than 2,0 m. Where the axle spread between one axle and its adjacent axle is greater than 2,0 m, each individual axle shall be considered as an independent axle group. |
2.39. | ‘Character of the vehicle’ means a descriptive term for a vehicle — tractor for semi-trailer, truck, bus, semi-trailer, full trailer, centre-axle trailer. |
2.40. | ‘Brake electric/electronic interface’ means the part of a separable electrical/electronic connection between the towing vehicle and the towed vehicle which is dedicated to the braking system. |
2.41. | ‘Automated connector’ means a system through which the electric and pneumatic connection, between the towing vehicle and towed vehicle is made automatically without direct intervention of a human operator. |
3. APPLICATION FOR APPROVAL
3.1. The application for approval of a vehicle type with regard to braking shall be submitted by the vehicle manufacturer or by his duly accredited representative.
3.2. It shall be accompanied by the under-mentioned documents in triplicate and by the following particulars:
3.2.1. | A description of the vehicle type with regard to the items specified in paragraph 2.2 above. The numbers and/or symbols identifying the vehicle type and, in the case of power-driven vehicles, the engine type shall be specified; |
3.2.2. | A list of the components, duly identified, constituting the braking system; |
3.2.3. | A diagram of assembled braking system and an indication of the position of its components on the vehicle; |
3.2.4. | Detailed drawings of each component to enable it to be easily located and identified. |
3.3. A vehicle, representative of the vehicle type to be approved, shall be submitted to the Technical Service conducting the approval tests.
3.4. The Type Approval Authority shall verify the existence of satisfactory arrangements for ensuring effective control of the conformity of production before type approval is granted.
4. APPROVAL
4.1. If the vehicle type submitted for approval pursuant to this Regulation meets the requirements of paragraphs 5 and 6 below, approval of that vehicle type shall be granted.
4.2. An approval number shall be assigned to each type approved, its first two digits (at present 11) shall indicate the series of amendments incorporating the most recent major technical amendments made to the Regulation at the time of issue of the approval. The same Contracting Party shall not assign the same number to the same vehicle type equipped with another type of braking system, or to another vehicle type.
4.3. Notice of approval or of refusal of approval of a vehicle type pursuant to this Regulation shall be communicated to the Parties to the Agreement applying this Regulation by means of a form conforming to the model in Annex 2 to this Regulation and of a summary of the information contained in the documents referred to in paragraphs 3.2.1 to 3.2.4 above, the drawings supplied by the applicant being in a format not exceeding A4 (210 × 297 mm), or folded to that format, and on an appropriate scale.
4.4. There shall be affixed, conspicuously and in a readily accessible place specified on the approval form, to every vehicle conforming to a vehicle type approved under this Regulation, an international approval mark consisting of:
4.4.1. | A circle surrounding the letter ‘E’ followed by the distinguishing number of the country which has granted approval (3), and |
4.4.2. | The number of this Regulation, followed by the letter ‘R’, a dash and the approval number to the right of the circle prescribed in paragraph 4.4.1 above. |
4.5. However, if a vehicle of categories M2 or M3 has been approved pursuant to the provisions of Annex 4, paragraph 1.8 to this Regulation, the number of the Regulation shall be followed by the letter M.
4.6. If the vehicle conforms to a vehicle type approved under one or more other Regulations, annexed to the Agreement, in the country which has granted approval under this Regulation, the symbol prescribed in paragraph 4.4.1 need not be repeated; in such a case, the Regulation and approval numbers and the additional symbols of all the Regulations under which approval has been granted in the country which has granted approval under this Regulation shall be placed in vertical columns to the right of the symbol prescribed in paragraph 4.4.1 above.
4.7. The approval mark shall be clearly legible and be indelible.
4.8. The approval mark shall be placed close to or on the vehicle data plate.
4.9. Annex 3 to this Regulation gives examples of arrangements of approval marks.
5. SPECIFICATIONS
5.1. General
5.1.1. Braking system
5.1.1.1. The braking system shall be so designed, constructed and fitted as to enable the vehicle in normal use, despite the vibration to which it may be subjected, to comply with the provisions of this Regulation.
5.1.1.2. In particular, the braking system shall be so designed, constructed and fitted as to be able to resist the corroding and ageing phenomena to which it is exposed.
5.1.1.3. Brake linings shall not contain asbestos.
5.1.1.4. The effectiveness of the braking systems, including the electric control line, shall not be adversely affected by magnetic or electrical fields. This shall be demonstrated by fulfilling the technical requirements and respecting the transitional provisions of Regulation No 10 by applying:
(a) | The 03 series of amendments for vehicles without a coupling system for charging the rechargeable energy storage system (traction batteries). |
(b) | The 04 series of amendments for vehicles with a coupling system for charging the rechargeable energy storage system (traction batteries). |
5.1.1.5. A failure detection signal may interrupt momentarily (< 10 ms) the demand signal in the control transmission, provided that the braking performance is thereby not reduced.
5.1.2. Functions of the braking system
The braking system defined in paragraph 2.3 of this Regulation shall fulfil the following functions:
5.1.2.1. | Service braking system The service braking system shall make it possible to control the movement of the vehicle and to halt it safely, speedily and effectively, whatever its speed and load, on any up or down gradient. It shall be possible to graduate this braking action. The driver shall be able to achieve this braking action from his driving seat without removing his hands from the steering control. |
5.1.2.2. | Secondary braking system The secondary braking system shall make it possible to halt the vehicle within a reasonable distance in the event of failure of the service braking system. It shall be possible to graduate this braking action. The driver shall be able to obtain this braking action from his driving seat while keeping at least one hand on the steering control. For the purposes of these provisions it is assumed that not more than one failure of the service braking system can occur at one time. |
5.1.2.3. | Parking braking system The parking braking system shall make it possible to hold the vehicle stationary on an up or down gradient even in the absence of the driver, the working parts being then held in the locked position by a purely mechanical device. The driver shall be able to achieve this braking action from his driving seat, subject, in the case of a trailer, to the provisions of paragraph 5.2.2.10 of this Regulation. The trailer air brake and the parking braking system of the towing vehicle may be operated simultaneously provided that the driver is able to check, at any time, that the parking brake performance of the vehicle combination, obtained by the purely mechanical action of the parking braking system, is sufficient. |
5.1.3. Connections, for compressed-air braking systems, between power-driven vehicles and trailers
5.1.3.1. The connections of the compressed-air braking systems between power-driven vehicles and trailers shall be provided according to paragraphs 5.1.3.1.1, 5.1.3.1.2 or 5.1.3.1.3:
5.1.3.1.1. | One pneumatic supply line and one pneumatic control line; |
5.1.3.1.2. | One pneumatic supply line, one pneumatic control line and one electric control line; |
5.1.3.1.3. | One pneumatic supply line and one electric control line; this option is subject to footnote (4). |
5.1.3.2. The electric control line of the power-driven vehicle shall provide information as to whether the requirements of paragraph 5.2.1.18.2 can be satisfied by the electric control line, without assistance from the pneumatic control line. It shall also provide information as to whether it is equipped according to paragraph 5.1.3.1.2 with two control lines or according to paragraph 5.1.3.1.3 with only an electric control line.
5.1.3.3. A power-driven vehicle equipped according to paragraph 5.1.3.1.3 shall recognise that the coupling of a trailer equipped according to paragraph 5.1.3.1.1 is not compatible. When such vehicles are electrically connected via the electric control line of the towing vehicle, the driver shall be warned by the red optical warning signal specified in paragraph 5.2.1.29.1.1 and when the system is energised, the brakes on the towing vehicle shall be automatically applied. This brake application shall provide at least the prescribed parking braking performance required by paragraph 2.3.1 of Annex 4 to this Regulation.
5.1.3.4. In the case of a power-driven vehicle equipped with two control lines as defined in paragraph 5.1.3.1.2, when electrically connected to a trailer which is also equipped with two control lines, the following provisions shall be fulfilled:
5.1.3.4.1. | Both signals shall be present at the coupling head and the trailer shall use the electric control signal unless this signal is deemed to have failed. In this case the trailer shall automatically switch to the pneumatic control line; |
5.1.3.4.2. | Each vehicle shall conform to the relevant provisions of Annex 10 to this Regulation for both electric and pneumatic control lines; and |
5.1.3.4.3. | When the electric control signal has exceeded the equivalent of 100 kPa for more than 1 second, the trailer shall verify that a pneumatic signal is present; should no pneumatic signal be present, the driver shall be warned from the trailer by the separate yellow warning signal specified in paragraph 5.2.1.29.2 below. |
5.1.3.5. A trailer may be equipped as defined in paragraph 5.1.3.1.3, provided that it can only be operated in conjunction with a power-driven vehicle with an electric control line which satisfies the requirements of paragraph 5.2.1.18.2. In any other case, the trailer, when electrically connected, shall automatically apply the brakes or remain braked. The driver shall be warned by the separate yellow warning signal specified in paragraph 5.2.1.29.2.
(a) | The electric control line shall conform to ISO 11992-1 and 11992-2:2003 including its amendment 1:2007 and be a point-to-point type using:
|
(b) | The data contacts of the ISO 7638 connector shall be used to transfer information exclusively for braking (including ABS) and running gear (steering, tyres and suspension) functions as specified in ISO 11992-2:2003 including its Amd.1:2007. The braking functions have priority and shall be maintained in the normal and failed modes. The transmission of running gear information shall not delay braking functions. |
(c) | The power supply, provided by the ISO 7638 connector, shall be used exclusively for braking and running gear functions and that required for the transfer of trailer related information not transmitted via the electric control line. However, in all cases the provisions of paragraph 5.2.2.18 of this Regulation shall apply. The power supply for all other functions shall use other measures. |
5.1.3.6.1. The support of messages defined within ISO 11992-2:2003 including Amd.1:2007 is specified within Annex 16 to this Regulation for the towing vehicle and trailer as appropriate.
5.1.3.6.2. The functional compatibility of towing and towed vehicles equipped with electric control lines as defined above shall be assessed at the time of type approval by checking that the relevant provisions of ISO 11992:2003, including ISO 11992-2:2003 and its Amd.1:2007 parts 1 and 2, are fulfilled. Annex 17 to this Regulation provides an example of tests that may be used to perform this assessment.
5.1.3.6.3. When a power-driven vehicle is equipped with an electric control line and electrically connected to a trailer equipped with an electric control line, a continuous failure (> 40 ms) within the electric control line shall be detected in the power-driven vehicle and shall be signalled to the driver by the yellow warning signal specified in paragraph 5.2.1.29.1.2, when such vehicles are connected via the electric control line.
5.1.3.7. If the operation of the parking braking system on the power-driven vehicle also operates a braking system on the trailer, as permitted by paragraph 5.1.2.3, then the following additional requirements shall be met:
5.1.3.7.1. | When the power-driven vehicle is equipped according to paragraph 5.1.3.1.1, the actuation of the parking brake system of the power-driven vehicle shall actuate a braking system on the trailer via the pneumatic control line. |
5.1.3.7.2. | When the power-driven vehicle is equipped according to paragraph 5.1.3.1.2, the actuation of the parking brake system on the power-driven vehicle shall actuate a braking system on the trailer as prescribed in paragraph 5.1.3.7.1. In addition, the actuation of the parking brake system may also actuate a braking system on the trailer via the electric control line. |
5.1.3.7.3. | When the power-driven vehicle is equipped according to paragraph 5.1.3.1.3 or, if it satisfies the requirements of paragraph 5.2.1.18.2 without assistance from the pneumatic control line, paragraph 5.1.3.1.2, the actuation of the parking braking system on the power-driven vehicle shall actuate a braking system on the trailer via the electric control line. When the electrical energy for the braking equipment of the power-driven vehicle is switched off, the braking of the trailer shall be effected by evacuation of the supply line (in addition, the pneumatic control line may remain pressurised); the supply line may only remain evacuated until the electrical energy for the braking equipment of the power-driven vehicle is restored and simultaneously the braking of the trailer via the electric control line is restored. |
5.1.3.8. Shut-off devices which are not automatically actuated shall not be permitted.
5.1.3.9. In the case of tractor and semi-trailer combinations, the flexible hoses and cables shall be a part of the power-driven vehicle. In all other cases, the flexible hoses and cables shall be a part of the trailer.
In the case of an automated connector, this requirement regarding the allocation of flexible hoses and cables is not applicable.
5.1.4. Provisions for the periodic technical inspection of braking systems
5.1.4.1. It shall be possible to assess the wear condition of the components of the service brake that are subject to wear e.g. friction linings and drums/discs (in the case of drums or discs, wear assessment may not necessarily be carried out at the time of periodic technical inspection). The method by which this may be realised is defined in paragraphs 5.2.1.11.2 and 5.2.2.8.2 of this Regulation.
5.1.4.2. For the purpose of determining the in-use braking forces of each axle of the vehicle, with a compressed-air braking system, air pressure test connections are required:
5.1.4.2.1. | In each independent circuit of the braking system, at the closest readily accessible position to the brake cylinder which is the least favourably placed as far as the response time described in Annex 6 is concerned. |
5.1.4.2.2. | In a braking system which incorporates a pressure modulation device as referred to in paragraph 7.2 of Annex 10, located in the pressure line upstream and downstream of this device at the closest accessible position. If this device is pneumatically controlled an additional test connection is required to simulate the laden condition. Where no such device is fitted, a single pressure test connection, equivalent to the downstream connector mentioned above, shall be provided. These test connections shall be so located as to be easily accessible from the ground or within the vehicle. |
5.1.4.2.3. | At the closest readily accessible position to the least favourably placed energy storage device within the meaning of paragraph 2.4 of Annex 7, section A. |
5.1.4.2.4. | In each independent circuit of the braking system so it is possible to check the input and output pressure of the complete transmission line. |
5.1.4.2.5. | The pressure test connections shall comply with clause 4 of ISO Standard 3583:1984. |
5.1.4.3. The accessibility of required pressure test connections shall not be obstructed by modifications and assembly of accessories or the vehicle body.
5.1.4.4. It shall be possible to generate maximum braking forces under static conditions on a rolling road or roller brake tester.
5.1.4.5. Data for braking systems:
5.1.4.5.1. | The data of the compressed-air braking system for the functional and efficiency test shall be specified at the vehicle in a visible position in indelible form, or made freely available in another way (e.g. handbook, electronic data record). |
5.1.4.5.2. | For vehicles equipped with compressed-air braking systems at least the following data are required: Pneumatic characteristic data:
|
5.1.4.6. Reference braking forces
5.1.4.6.1. Reference braking forces shall be defined for vehicles with compressed air operated brakes using a roller brake tester.
5.1.4.6.2. Reference braking forces are to be determined for a brake actuator pressure range from 100 kPa to the pressure generated under Type-0 conditions for each axle. The applicant for type approval shall nominate reference-braking forces for a brake activator pressure range from 100 kPa. These data shall be made available, by the vehicle manufacturer, according to paragraph 5.1.4.5.1 above.
5.1.4.6.3. The reference braking forces shall be declared such that the vehicle is capable of generating a braking rate equivalent to that defined in Annex 4 of this Regulation for the relevant vehicle (50 per cent in the case of vehicles of category M2, M3, N2, N3, O3 and O4 except semi-trailers, 45 per cent in the case of semi-trailers), whenever the measured roller braking force, for each axle irrespective of load, is not less than the reference braking force for a given brake actuator pressure within the declared operating pressure range (9).
5.1.4.7. It shall be possible to verify, in a frequent and simple way, the correct operational status of those complex electronic systems which have control over braking. If special information is needed, this shall be made freely available.
5.1.4.7.1. Where the operational status is indicated to the driver by warning signals, as specified in this Regulation, it shall be possible at a periodic technical inspection to confirm the correct operational status by visual observation of the warning signals following a power-on.
5.1.4.7.2. At the time of type approval, the means implemented to protect against simple unauthorised modification of the operation to the verification means chosen by the manufacturer (e.g. warning signal) shall be confidentially outlined.
Alternatively, this protection requirement is fulfilled when a secondary means of checking the correct operational status is available.
5.1.5. The requirements of Annex 18 shall be applied to the safety aspects of all complex electronic vehicle control systems which provide or form part of the control transmission of the braking function included those which utilise the braking system(s) for automatically commanded braking or selective braking.
However, systems or functions, which use the braking system as the means of achieving a higher level objective, are subject to Annex 18 only insofar as they have a direct effect on the braking system. If such systems are provided, they shall not be deactivated during type approval testing of the braking system.
5.2. Characteristics of braking systems
5.2.1. Vehicles of categories M2, M3 and N
5.2.1.1. The set of braking systems with which a vehicle is equipped shall satisfy the requirements laid down for service, secondary and parking braking systems.
5.2.1.2. The systems providing service, secondary and parking braking may have common components so long as they fulfil the following conditions:
5.2.1.2.1. | There shall be at least two controls, independent of each other and readily accessible to the driver from his normal driving position. For all categories of vehicles, except M2 and M3, every brake control (excluding an endurance braking system control) shall be designed such that it returns to the fully off position when released. This requirement shall not apply to a parking brake control (or that part of a combined control) when it is mechanically locked in an applied position; |
5.2.1.2.2. | The control of the service braking system shall be independent of the control of the parking braking system; |
5.2.1.2.3. | If the service braking system and the secondary braking system have the same control, the effectiveness of the linkage between that control and the different components of the transmission systems shall not be liable to diminish after a certain period of use; |
5.2.1.2.4. | If the service braking system and the secondary braking system have the same control, the parking braking system shall be so designed that it can be actuated when the vehicle is in motion. This requirement shall not apply if the vehicle's service braking system can be actuated, even partially, by means of an auxiliary control; |
5.2.1.2.5. | Without prejudice to the requirements of paragraph 5.1.2.3 of this Regulation, the service braking system and the parking braking system may use common components in their transmission(s), provided that in the event of a failure in any part of the transmission(s) the requirements for secondary braking are still ensured; |
5.2.1.2.6. | In the event of breakage of any component other than the brakes (as defined in paragraph 2.6 of this Regulation) or the components referred to in paragraph 5.2.1.2.8 below, or of any other failure of the service braking system (malfunction, partial or total exhaustion of an energy reserve), the secondary braking system or that part of the service braking system which is not affected by the failure, shall be able to bring the vehicle to a halt in the conditions prescribed for secondary braking; |
5.2.1.2.7. | In particular, where the secondary braking system and the service braking system have a common control and a common transmission:
|
5.2.1.2.8. | Certain parts, such as the pedal and its bearing, the master cylinder and its piston or pistons (hydraulic systems), the control valve (hydraulic and/or pneumatic systems), the linkage between the pedal and the master cylinder or the control valve, the brake cylinders and their pistons (hydraulic and/or pneumatic systems), and the lever-and-cam assemblies of brakes, shall not be regarded as liable to breakage if they are amply dimensioned, are readily accessible for maintenance, and exhibit safety features at least equal to those prescribed for other essential components (such as the steering linkage) of the vehicle. Any such part as aforesaid whose failure would make it impossible to brake the vehicle with a degree of effectiveness at least equal to that prescribed for secondary braking shall be made of metal or of a material with equivalent characteristics and shall not undergo notable distortion in normal operation of the braking systems. |
5.2.1.3. Where there are separate controls for the service braking system and the secondary braking system, simultaneous actuation of the two controls shall not render both the service braking system and the secondary braking system inoperative, either when both braking systems are in good working order or when one of them is faulty.
5.2.1.4. The service braking system shall, whether or not it is combined with the secondary braking system, be such that in the event of failure in a part of its transmission a sufficient number of wheels are still braked by actuation of the service brake control; these wheels shall be so selected that the residual performance of the service braking system satisfies the requirements laid down in paragraph 2.4 of Annex 4 to this Regulation.
5.2.1.4.1. However, the foregoing provisions shall not apply to tractor vehicles for semi-trailers when the transmission of the semi-trailer's service braking system is independent of that of the tractor vehicle's service braking system;
5.2.1.4.2. The failure of a part of a hydraulic transmission system shall be signalled to the driver by a device comprising a red warning signal, as specified in paragraph 5.2.1.29.1.1. Alternatively, the lighting up of this device when the fluid in the reservoir is below a certain level specified by the manufacturer shall be permitted.
5.2.1.5. Where use is made of energy other than the muscular energy of the driver, there need not be more than one source of such energy (hydraulic pump, air compressor, etc.), but the means by which the device constituting that source is driven shall be as safe as practicable.
5.2.1.5.1. In the event of failure in any part of the transmission of a braking system, the feed to the part not affected by the failure shall continue to be ensured if required for the purpose of halting the vehicle with the degree of effectiveness prescribed for residual and/or secondary braking. This condition shall be met by means of devices which can be easily actuated when the vehicle is stationary, or by automatic means.
5.2.1.5.2. Furthermore, storage devices located down-circuit of this device shall be such that in the case of a failure in the energy supply after four full-stroke actuations of the service brake control, under the conditions prescribed in paragraph 1.2 of Annex 7 to this Regulation, it is still possible to halt the vehicle at the fifth application, with the degree of effectiveness prescribed for secondary braking.
5.2.1.5.3. However, for hydraulic braking systems with stored energy, these provisions can be considered to be met provided that the requirements of paragraph 1.2.2 of Part C of Annex 7 to this Regulation, are satisfied.
5.2.1.6. The requirements of paragraphs 5.2.1.2, 5.2.1.4 and 5.2.1.5 of this Regulation shall be met without the use of any automatic device of a kind such that its ineffectiveness might pass unnoticed through the fact that parts normally in a position of rest come into action only in the event of failure in the braking system.
5.2.1.7. The service braking system shall act on all wheels of the vehicle and shall distribute its action appropriately among the axles.
5.2.1.7.1. In the case of vehicles with more than two axles, in order to avoid wheel-locking or glazing of the brake linings, the brake force on certain axles may be reduced to zero automatically when carrying a much reduced load, provided that the vehicle meets all the performance requirements prescribed in Annex 4 to this Regulation.
5.2.1.7.2. In the case of N1 category vehicles with electric regenerative braking systems of category B, the braking input from other sources of braking, may be suitably phased to allow the electric regenerative braking system alone to be applied, provided that both the following conditions are met:
5.2.1.7.2.1. | Intrinsic variations in the torque output of the electrical regenerative braking system (e.g. as a result of changes in the electric state of charge in the traction batteries) are automatically compensated by appropriate variation in the phasing relationship as long as the requirements (10) of one of the following annexes to this Regulation are satisfied:
|
5.2.1.7.2.2. | Wherever necessary, to ensure that braking rate (10) remains related to the driver's braking demand, having regard to the available tyre/road adhesion, braking shall automatically be caused to act on all wheels of the vehicle. |
5.2.1.8. The action of the service braking system shall be distributed between the wheels of one and the same axle symmetrically in relation to the longitudinal median plane of the vehicle. Compensation and functions, such as anti-lock, which may cause deviations from this symmetrical distribution, shall be declared.
5.2.1.8.1. Compensation by the electric control transmission for deterioration or defect within the braking system shall be indicated to the driver by means of the yellow warning signal specified in paragraph 5.2.1.29.1.2. This requirement shall apply for all conditions of loading when compensation exceeds the following limits:
5.2.1.8.1.1. | A difference in transverse braking pressures on any axle of:
|
5.2.1.8.1.2. | An individual compensating value on any axle of:
|
5.2.1.8.2. Compensation as defined above, is permitted only when the initial brake application is made at vehicle speeds greater than 10 km/h.
5.2.1.9. Malfunctions of the electric control transmission shall not apply the brakes contrary to the driver's intentions.
5.2.1.10. The service, secondary and parking braking systems shall act on braking surfaces connected to the wheels through components of adequate strength.
Where braking torque for a particular axle or axles is provided by both a friction braking system and an electrical regenerative braking system of category B, disconnection of the latter source is permitted, providing that the friction braking source remains permanently connected and able to provide the compensation referred to in paragraph 5.2.1.7.2.1.
However in the case of short disconnection transients, incomplete compensation is accepted, but within 1 s, this compensation shall have attained at least 75 per cent of its final value.
Nevertheless, in all cases the permanently connected friction braking source shall ensure that both the service and secondary braking systems continue to operate with the prescribed degree of effectiveness.
Disconnection of the braking surfaces of the parking braking system shall be permitted only on condition that the disconnection is controlled exclusively by the driver from his driving seat, by a system incapable of being brought into action by a leak.
5.2.1.11. Wear of the brakes shall be capable of being easily taken up by means of a system of manual or automatic adjustment. In addition, the control and the components of the transmission and of the brakes shall possess a reserve of travel and, if necessary, suitable means of compensation such that, when the brakes become heated, or the brake linings have reached a certain degree of wear, effective braking is ensured without immediate adjustment being necessary.
5.2.1.11.1. Wear adjustment shall be automatic for the service brakes. However, the fitting of automatic brake adjustment devices is optional for off-road vehicles of categories N2 and N3 and for the rear brakes of vehicles of category N1. Brakes equipped with automatic brake adjustment devices shall, after heating followed by cooling, be capable of free running as defined in paragraph 1.5.4 of Annex 4 following the Type-I test also defined in that annex.
5.2.1.11.2. Checking the wear of the service brake friction components
5.2.1.11.2.1. It shall be possible to easily assess this wear on service brake linings from the outside or underside of the vehicle, without the removal of the wheels, by the provision of appropriate inspection holes or by some other means. This may be achieved by utilising simple standard workshop tools or common inspection equipment for vehicles.
Alternatively, a sensing device per wheel (twin wheels are considered as a single wheel), which will warn the driver at his driving position when lining replacement is necessary, is acceptable. In the case of an optical warning, the yellow warning signal specified in paragraph 5.2.1.29.1.2 below may be used.
5.2.1.11.2.2. Assessment of the wear condition of the friction surfaces of brake discs or drums may only be performed by direct measurement of the actual component or examination of any brake disc or drum wear indicators, which may necessitate some level of disassembly. Therefore, at the time of type approval, the vehicle manufacturer shall define the following:
(a) | The method by which wear of the friction surfaces of drums and discs may be assessed, including the level of disassembly required and the tools and process required to achieve this; |
(b) | Information defining the maximum acceptable wear limit at the point at which replacement becomes necessary. |
This information shall be made freely available, e.g. vehicle handbook or electronic data record.
5.2.1.12. In hydraulic-transmission braking systems, the filling ports of the fluid reservoirs shall be readily accessible; in addition, the receptacles containing the reserve fluid shall be so designed and constructed that the level of the reserve fluid can be easily checked without the receptacles having to be opened. If this latter condition is not fulfilled, the red warning signal specified in paragraph 5.2.1.29.1.1 shall draw the driver's attention to any fall in the level of reserve fluid liable to cause a failure of the braking system. The type of fluid to be used in the hydraulic transmission braking systems shall be identified by the symbol in accordance with figure 1 or 2 of Standard ISO 9128:2006. The symbol shall be affixed in a visible position in indelible form within 100 mm of the filling ports of the fluid reservoirs; additional information may be provided by the manufacturer.
5.2.1.13. Warning device
5.2.1.13.1. Any vehicle fitted with a service brake actuated from an energy reservoir shall, where the prescribed secondary braking performance cannot be obtained by means of this braking system without the use of the stored energy, be provided with a warning device, in addition to a pressure gauge, where fitted, giving an optical or acoustic signal when the stored energy, in any part of the system, falls to a value at which without re-charging of the reservoir and irrespective of the load conditions of the vehicle, it is possible to apply the service brake control a fifth time after four full-stroke actuations and obtain the prescribed secondary braking performance (without faults in the service brake transmission and with the brakes adjusted as closely as possible). This warning device shall be directly and permanently connected to the circuit. When the engine is running under normal operating conditions and there are no faults in the braking system, as is the case in approval tests for this type, the warning device shall give no signal except during the time required for charging the energy reservoir(s) after start-up of the engine. The red warning signal specified in paragraph 5.2.1.29.1.1 shall be used as the optical warning signal.
5.2.1.13.1.1. However, in the case of vehicles which are only considered to comply with the requirements of paragraph 5.2.1.5.1 of this Regulation by virtue of meeting the requirements of paragraph 1.2.2 of Part C of Annex 7 to this Regulation, the warning device shall consist of an acoustic signal in addition to an optical signal. These devices need not operate simultaneously, provided that each of them meet the above requirements and the acoustic signal is not actuated before the optical signal. The red warning signal specified in paragraph 5.2.1.29.1.1 shall be used as the optical warning signal.
5.2.1.13.1.2. This acoustic device may be rendered inoperative while the handbrake is applied and/or, at the choice of the manufacturer, in the case of automatic transmission the selector is in the ‘Park’ position.
5.2.1.14. Without prejudice to the requirements of paragraph 5.1.2.3 of this Regulation, where an auxiliary source of energy is essential to the functioning of a braking system, the reserve of energy shall be such as to ensure that, if the engine stops or in the event of a failure of the means by which the energy source is driven, the braking performance remains adequate to bring the vehicle to a halt in the prescribed conditions. In addition, if the muscular effort applied by the driver to the parking braking system is reinforced by a servo device, the actuation of the parking braking system shall be ensured in the event of a failure of the servo device, if necessary by using a reserve of energy independent of that normally supplying the servo device. This reserve of energy may be that intended for the service braking system.
5.2.1.15. In the case of a power-driven vehicle to which the coupling of a trailer equipped with a brake controlled by the driver of the towing vehicle is authorised, the service braking system of the towing vehicle shall be equipped with a device so designed that in the event of failure of the trailer's braking system, or in the event of an interruption in the air supply pipe (or of such other type of connection as may be adopted) between the towing vehicle and its trailer, it shall still be possible to brake the towing vehicle with the effectiveness prescribed for secondary braking; it is accordingly prescribed, in particular, that this device shall be situated on the towing vehicle.
5.2.1.16. The pneumatic/hydraulic auxiliary equipment shall be supplied with energy in such a way that during its operation, the prescribed deceleration values can be reached and that even in the event of damage to the source of energy the operation of the auxiliary equipment cannot cause the reserves of energy feeding the braking systems to fall below the level indicated in paragraph 5.2.1.13 above.
5.2.1.17. If the trailer is of category O3 or O4, the service braking system shall be of the continuous or semi-continuous type.
5.2.1.18. In the case of a vehicle authorised to tow a trailer of category O3 or O4, its braking systems shall satisfy the following conditions:
5.2.1.18.1. | When the towing vehicle's secondary braking system comes into action, there shall also be a graduated braking action in the trailer; |
5.2.1.18.2. | In the event of failure of the towing vehicle's service braking system, where that system consists of at least two independent parts, the part or parts not affected by the failure shall be capable of partially or fully actuating the brakes of the trailer. It shall be possible to graduate this braking action. If this operation is achieved by a valve which is normally at rest, then such a valve may only be incorporated if its correct functioning can easily be checked by the driver, either from within the cab or from outside the vehicle, without the use of tools; |
5.2.1.18.3. | In the event of a failure (e.g. breakage or leak) in one of the pneumatic connecting lines, interruption or defect in the electric control line, it shall nevertheless be possible for the driver, fully or partially, to actuate the brakes of the trailer by means either of the service braking control or of the secondary braking control or of the parking braking control, unless the failure automatically causes the trailer to be braked with the performance prescribed in paragraph 3.3 of Annex 4 to this Regulation. |
5.2.1.18.4. | The automatic braking in paragraph 5.2.1.18.3 above shall be considered to be met when the following conditions are fulfilled:
|
5.2.1.18.5. | In the event of a failure in one of the control lines connecting two vehicles equipped according to paragraph 5.1.3.1.2, the control line not affected by the failure shall automatically ensure the braking performance prescribed for the trailer in paragraph 3.1 of Annex 4. |
5.2.1.19. In the case of a power-driven vehicle equipped to draw a trailer with an electrical braking system, according to paragraph 1.1 of Annex 14 to this Regulation, the following requirements shall be met:
5.2.1.19.1. | The power supply (generator and battery) of the power-driven vehicle shall have a sufficient capacity to provide the current for an electrical braking system. With the engine running at the idling speed recommended by the manufacturer and all electrical devices supplied by the manufacturer as standard equipment of the vehicle switched on, the voltage in the electrical lines shall at maximum current consumption of the electrical braking system (15 A) not fall below the value of 9,6 V measured at the connection. The electrical lines shall not be capable of short circuiting even when overloaded; |
5.2.1.19.2. | In the event of a failure in the towing vehicle's service braking system, where that system consists of at least two independent parts, the part or parts not affected by the failure should be capable of partially or fully actuating the brakes of the trailer; |
5.2.1.19.3. | The use of the stop-lamp switch and circuit for actuating the electrical braking system is permissible only if the actuating line is connected in parallel with the stop-lamp and the existing stop-lamp switch and circuit are capable of taking the extra load. |
5.2.1.20. In the case of a pneumatic service braking system comprising two or more independent sections, any leakage between those sections at or downstream of the control shall be continuously vented to atmosphere.
5.2.1.21. In the case of a power-driven vehicle authorised to tow a trailer of categories O3 or O4, the service braking system of the trailer may only be operated in conjunction with the service, secondary or parking braking system of the towing vehicle. However, automatic application of the trailer brakes alone is permitted where the operation of the trailer brakes is initiated automatically by the towing vehicle for the sole purpose of vehicle stabilisation.
5.2.1.22. Power-driven vehicles of categories M2, M3, N2 and N3 with not more than four axles shall be equipped with anti-lock systems of category 1 in accordance with Annex 13 to this Regulation.
5.2.1.23. Power driven vehicles authorised to tow a trailer equipped with an anti-lock system shall also be equipped with either one or both of the following, for the electric control transmission:
(a) | A special electrical connector conforming to ISO 7638:2003 (11); |
(b) | An automated connector meeting the requirements specified in Annex 22. |
5.2.1.24. Additional requirements for vehicles of categories M2, N1 and category N2 < 5 tonnes equipped with an electric regenerative braking system of category A:
5.2.1.24.1. | The electric regenerative braking shall only be actuated by the accelerator control and/or the gear selector neutral position for vehicles of category N1. |
5.2.1.24.2. | In addition, for vehicles of categories M2 and N2 (< 5 tonnes), the electric regenerative braking control can be a separate switch or lever. |
5.2.1.24.3. | The requirements of paragraphs 5.2.1.25.6 and 5.2.1.25.7 also apply to Category A regenerative braking systems. |
5.2.1.25. Additional requirements for vehicles of Categories M2, N1, and N2 < 5 tonnes fitted with an electric regenerative braking system of category B:
5.2.1.25.1. | It shall not be possible to disconnect, partially or totally, one part of the service braking system other than by automatic means. This should not be construed as a departure from the requirements of paragraph 5.2.1.10. |
5.2.1.25.2. | The service braking system shall have only one control device. |
5.2.1.25.3. | For vehicles fitted with electric regenerative braking systems of both categories, all the relevant prescriptions shall apply except paragraph 5.2.1.24.1. In this case, the electric regenerative braking may be actuated by the accelerator control and/or the gear selector neutral position for vehicles of category N1. Additionally, the action on the service braking control shall not reduce the above braking effect generated by the release of accelerator control. |
5.2.1.25.4. | The service braking system shall not be adversely affected by the disengagement of the motor(s) or by the gear ratio used. |
5.2.1.25.5. | If the operation of the electric component of braking is ensured by a relation established between the information coming from the control of the service brake and the braking force at the respective wheels, a failure of this relation leading to the modification of the braking distribution among the axles (Annex 10 or 13, whichever is applicable) shall be signalled to the driver by an optical warning signal at the latest at the moment when the control is actuated and this signal shall remain lit as long as this defect exists and that the vehicle control switch (key) is in the ‘ON’ position. |
5.2.1.25.6. | The operation of the electric regenerative braking shall not be adversely affected by magnetic or electric fields. |
5.2.1.25.7. | For vehicles equipped with an anti-lock device, the anti-lock device shall control the electric regenerative braking system. |
5.2.1.26. Special additional requirements for the electric transmission of the parking braking system
5.2.1.26.1. In the case of a failure within the electric transmission, any unintended actuation of the parking braking system shall be prevented.
5.2.1.26.2. The following requirements shall be fulfilled in the event of an electrical failure as specified:
5.2.1.26.2.1. | Vehicles of categories M2, M3, N2 and N3: In the case of an electrical failure in the control or a break in the wiring within the electric control transmission external to the electronic control unit(s), excluding the energy supply, it shall remain possible to apply the parking braking system from the driver's seat and thereby be capable of holding the laden vehicle stationary on an 8 per cent up or down gradient. Alternatively, in this case, an automatic actuation of the parking brake is allowed when the vehicle is stationary, provided that the above performance is achieved and, once applied, the parking brake remains engaged independently of the status of the ignition (start) switch. In this alternative, the parking brake shall be automatically released as soon as the driver starts to set the vehicle in motion again. It shall also be possible to release the parking braking system, if necessary by the use of tools and/or an auxiliary device carried/fitted on the vehicle. |
5.2.1.26.2.2. | Vehicles of category N1: In the case of an electrical failure in the control or a break in the wiring within the electric control transmission between the control and the ECU directly connected with it, excluding the energy supply, it shall remain possible to apply the parking braking system from the driver's seat and thereby be capable of holding the laden vehicle stationary on an 8 per cent up or down gradient. Alternatively, in this case, an automatic actuation of the parking brake is allowed when the vehicle is stationary, provided that the above performance is achieved and, once applied, the parking brake remains engaged independently of the status of the ignition (start) switch. In this alternative, the parking brake shall be automatically released as soon as the driver starts to set the vehicle in motion again. The engine/manual transmission or the automatic transmission (park position) may be used to achieve or assist in achieving the above performance. |
5.2.1.26.2.3. | A break in the wiring within the electric transmission, or an electric failure in the control of the parking braking system shall be signalled to the driver by the yellow warning signal specified in paragraph 5.2.1.29.1.2. When caused by a break in the wiring within the electric control transmission of the parking braking system, this yellow warning signal shall be signalled as soon as the break occurs. In addition, such an electric failure in the control or break in the wiring external to the electronic control unit(s) and excluding the energy supply shall be signalled to the driver by flashing the red warning signal specified in paragraph 5.2.1.29.1.1 as long as the ignition (start) switch is in the ‘on’ (run) position including a period of not less than 10 seconds thereafter and the control is in the ‘on’ (activated) position. However, if the parking braking system detects correct clamping of the parking brake, the flashing of the red warning signal may be suppressed and the non-flashing red signal shall be used to indicate parking brake applied. Where actuation of the parking brake is normally indicated by a separate red warning signal, satisfying all the requirements of 5.2.1.29.3, this signal shall be used to satisfy the above requirement for a red signal. |
5.2.1.26.3. Auxiliary equipment may be supplied with energy from the electric transmission of the parking braking system provided that the supply of energy is sufficient to allow the actuation of the parking braking system in addition to the vehicle electrical load under non-fault conditions. In addition, where the energy reserve is also used by the service braking system, the requirements of paragraph 5.2.1.27.7 shall apply.
5.2.1.26.4. After the ignition/start switch which controls the electrical energy for the braking equipment has been switched off and/or the key removed, it shall remain possible to apply the parking braking system, whereas releasing shall be prevented.
5.2.1.27. Special additional requirements for service braking systems with electric control transmission
5.2.1.27.1. With the parking brake released, the service braking system shall be able to generate a static total braking force at least equivalent to that required by the prescribed Type-0 test, even when the ignition/start switch has been switched off and/or the key has been removed. In the case of power-driven vehicles authorised to tow trailers of category O3 or O4, such vehicles shall provide a full control signal for the service braking system of the trailer. It should be understood that sufficient energy is available in the energy transmission of the service braking system.
5.2.1.27.2. In the case of a single temporary failure (< 40 ms) within the electric control transmission, excluding its energy supply, (e.g. non-transmitted signal or data error) there shall be no distinguishable effect on the service braking performance.
5.2.1.27.3. A failure within the electric control transmission (12), not including its energy reserve, that affects the function and performance of systems addressed in this Regulation shall be indicated to the driver by the red or yellow warning signal specified in paragraphs 5.2.1.29.1.1 and 5.2.1.29.1.2, respectively, as appropriate. When the prescribed service braking performance can no longer be achieved (red warning signal), failures resulting from a loss of electrical continuity (e.g. breakage, disconnection) shall be signalled to the driver as soon as they occur, and the prescribed residual braking performance shall be fulfilled by operating the service braking control in accordance with paragraph 2.4 of Annex 4 to this Regulation. These requirements shall not be construed as a departure from the requirements concerning secondary braking.
5.2.1.27.4. A power-driven vehicle, electrically connected to a trailer via an electric control line, shall provide a clear warning to the driver whenever the trailer provides the failure information that the stored energy in any part of the service braking system on the trailer falls below the warning level, as specified in paragraph 5.2.2.16 below. A similar warning shall also be provided when a continuous failure (> 40 ms) within the electric control transmission of the trailer, excluding its energy reserve, precludes achievement of the prescribed service braking performance of the trailer, as specified in paragraph 5.2.2.15.2.1 below. The red warning signal specified in paragraph 5.2.1.29.2.1 shall be used for this purpose.
5.2.1.27.5. In the event of a failure of the energy source of the electric control transmission, starting from the nominal value of the energy level, the full control range of the service braking system shall be guaranteed after twenty consecutive full stroke actuations of the service braking control. During the test, the braking control shall be fully applied for 20 seconds and released for 5 seconds on each actuation. It should be understood that during the above test, sufficient energy is available in the energy transmission to ensure full actuation of the service braking system. This requirement shall not be construed as a departure from the requirements of Annex 7.
5.2.1.27.6. When the battery voltage falls below a value nominated by the manufacturer at which the prescribed service braking performance can no longer be guaranteed and/or which precludes at least two independent service braking circuits from each achieving the prescribed secondary or residual braking performance, the red warning signal specified in paragraph 5.2.1.29.1.1 shall be activated. After the warning signal has been activated, it shall be possible to apply the service braking control and obtain at least the residual performance prescribed in paragraph 2.4 of Annex 4 to this Regulation. It should be understood that sufficient energy is available in the energy transmission of the service braking system. This requirement shall not be construed as a departure from the requirement concerning secondary braking.
5.2.1.27.7. If auxiliary equipment is supplied with energy from the same reserve as the electric control transmission, it shall be ensured that, with the engine running at a speed not greater than 80 per cent of the maximum power speed, the supply of energy is sufficient to fulfil the prescribed deceleration values by either provision of an energy supply which is able to prevent discharge of this reserve when all auxiliary equipment is functioning or by automatically switching off pre-selected parts of the auxiliary equipment at a voltage above the critical level referred to in paragraph 5.2.1.27.6 of this Regulation such that further discharge of this reserve is prevented. Compliance may be demonstrated by calculation or by a practical test. For vehicles authorised to tow a trailer of category O3 or O4 the energy consumption of the trailer shall be taken into account by a load of 400 W. This paragraph does not apply to vehicles where the prescribed deceleration values can be reached without the use of electrical energy.
5.2.1.27.8. If the auxiliary equipment is supplied with energy from the electric control transmission, the following requirements shall be fulfilled.
5.2.1.27.8.1. In the event of a failure in the energy source, whilst the vehicle is in motion, the energy in the reservoir shall be sufficient to actuate the brakes when the control is applied.
5.2.1.27.8.2. In the event of a failure in the energy source, whilst the vehicle is stationary and the parking braking system applied, the energy in the reservoir shall be sufficient to actuate the lights even when the brakes are applied.
5.2.1.27.9. In the case of a failure in the electric control transmission of the service braking system of a towing vehicle equipped with an electric control line according to paragraph 5.1.3.1.2 or 5.1.3.1.3, the full actuation of the brakes of the trailer shall remain ensured.
5.2.1.27.10. In the case of a failure in the electric control transmission of a trailer, electrically connected via an electric control line only, according to paragraph 5.1.3.1.3, braking of the trailer shall be ensured according to paragraph 5.2.1.18.4.1. This shall be the case whenever the trailer provides the ‘supply line braking request’ signal via the data communication part of the electric control line or in the event of the continuous absence of this data communication. This paragraph shall not apply to power-driven vehicles which cannot be operated with trailers connected via an electric control line only, as described in paragraph 5.1.3.5.
5.2.1.28. Special requirements for coupling force control
5.2.1.28.1. Coupling force control shall only be permitted in the towing vehicle.
5.2.1.28.2. The action of the coupling force control shall be to reduce the difference between the dynamic braking rates of towing and towed vehicles. The operation of the coupling force control shall be checked at the time of type approval. The method by which this check is carried out shall be agreed between the vehicle manufacturer and the technical service with the method of assessment and results being appended to the type approval report.
5.2.1.28.2.1. The coupling force control may control the braking rate TM/PM and/or the brake demand value(s) for the trailer. In the case of a towing vehicle equipped with two control lines according to paragraph 5.1.3.1.2 above, both signals shall be subject to similar control adjustments.
5.2.1.28.2.2. The coupling force control shall not prevent the maximum possible braking pressure(s) from being applied.
5.2.1.28.3. The vehicle shall fulfil the laden compatibility requirements of Annex 10, but to achieve the objectives of paragraph 5.2.1.28.2 the vehicle may deviate from these requirements when the coupling force control is in operation.
5.2.1.28.4. A coupling force control failure shall be detected and indicated to the driver by a yellow warning signal such as that specified in paragraph 5.2.1.29.1.2. In the event of a failure the relevant requirements of Annex 10 shall be fulfilled.
5.2.1.28.5. Compensation by the coupling force control system shall be indicated by means of the yellow warning signal specified in paragraph 5.2.1.29.1.2 if this compensation exceeds 150 kPa away from the nominal demand value defined in paragraph 2.28.3 up to a limit, in pm, of 650 kPa (or the equivalent digital demand). Above the level of 650 kPa the warning shall be given if the compensation causes the operating point to lie outside the laden compatibility band as specified in Annex 10 for the motor vehicle.
Diagram 1
Towing vehicles for trailers (except semi-trailers)
托管标准,您可以接收以下服务:
1 标准定期系统查新,若有最新版本,会以站内短信或邮件的形式通知用户;
2 随时在标准托管页面中查看到该条标准的最新状态;
3 若用户有在学习和科研中的需要,可以在标准托管页面中试阅标准;
4 企业如果需要上新产品,我院及时提供标准查询、采购等方面的支持;
5 为企业在标准制修订、企业良好行为创建以及标准化试点过程中遇到的困难,可联系我院指定相关专家负责进行指导帮助、提供政策咨询;
6 为企业提供标准化政策的解读、标准化知识的推广培训、标准自我公开声明、标准文献的免费查询、企业标准化体系建设等方面的标准化服务;
标准资讯点击排行榜 全部
资讯标题点击
[[ n.title ]] [[ n.read ]]大连标准化公共服务平台
版权:大连标准化研究院有限公司
地址:大连市中山区高原街56号
电话:0411-82740851
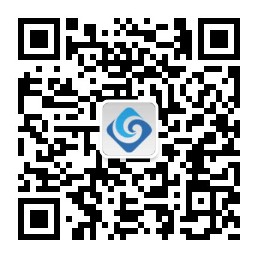